Warehouse Management Guide: Optimize Your Supply Chain
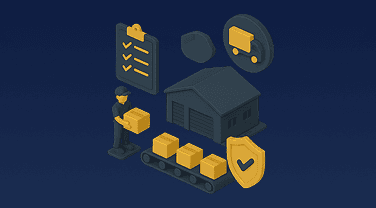
Table of Contents
Have you ever wondered what really happens when warehouse operations fail to synchronize with the rest of the supply chain? When systems upstream and downstream are disconnected, it doesn’t just confuse—it can lead to missed deliveries, rising costs, and unhappy customers. And let’s be honest, no business can afford that kind of chaos.
That’s why having a solid warehouse management system (WMS) isn’t just helpful—it’s essential. The global WMS market was valued at $3.94 billion in 2023, and it's expected to grow at an impressive 19.5% annually through 2030. Clearly, businesses everywhere are realizing the power of intelligent warehouse management.
A well-managed warehouse is more than just organized shelves and quick packing— it’s the heart of a smooth supply chain. It keeps inventory in check, speeds up fulfillment, and most importantly, keeps your customers happy. With the right WMS in place, everything flows—from the moment an order is placed to the second it lands at your customer’s doorstep.
If you're serious about scaling your business and keeping your operations sharp, investing in a great warehouse management system is a no-brainer.
In this guide, we’ll walk you through the essentials of optimizing your warehouse. We’ll explore common pain points, proven strategies, and how a robust solution like Omniful can help you reduce costs, increase efficiency, and elevate your operations to the next level.
Decoding the Concept of Warehouse Management
Think of warehouse management as the backbone of your supply chain—the part that keeps everything running smoothly behind the scenes. It’s all about managing the space where your inventory is stored and where orders are picked, packed, and shipped to your customers.
When warehouse operations aren’t handled well, things can quickly spiral—stock gets miscounted, orders are delayed, and resources go to waste. And that can mean unhappy customers and lost sales.
At its core, warehouse management involves overseeing the day-to-day activities that occur within a warehouse. This includes how goods are stored, moved, tracked, and ultimately dispatched out the door.
Key Responsibilities:
Some of them include:
- Inventory management – Keeping tabs on what’s in stock and making sure items are available when needed.
- Order fulfillment – Selecting the right products, packing them securely, and preparing them for shipment.
- Shipping and receiving – Handling incoming and outgoing deliveries to avoid bottlenecks or delays.
A well-managed warehouse doesn’t just help get products out faster—it supports the entire supply chain, from supplier to customer. It ensures that everything connects seamlessly, both upstream and downstream.
Understanding the Basics of a WMS
While there are instances of completely automated warehouses today, it all begins with a warehouse management system or WMS. A WMS is a software solution designed to fine-tune and streamline warehouse processes.
Today's top warehouse management systems automate all the essential tasks, handling your entire warehouse workflow. These include inventory tracking and updates, stock replenishment, order picking and packing, shipping, and fulfillment, among others. A WMS minimizes errors and enhances productivity by providing real-time visibility into stock levels, order status, and labor utilization.
With special inbound and outbound functions, a warehouse management system enables businesses to track all order statuses in real-time. Furthermore, smart picking allows warehouse personnel to easily optimize routes and schedules, thereby reducing lead times and increasing order accuracy.
Why Your Business Needs a Warehouse Management System?
Even the best warehouse management systems can't do it all on their own. They connect with all other enterprise systems and fetch the correct order data while sharing relevant details with other systems across the supply chain to ensure timely delivery.
If you manage omnichannel orders sourced from multiple hubs and warehouses, you will likely encounter significant complexity in ensuring orders are in stock and at the right locations. Monitoring such operations is impossible without a quality WMS.
A warehouse management system addresses some of the most common challenges across supply chain operations:
1. Inventory Inaccuracies & Stockouts
Inaccurate inventory counts are a common reason for missed opportunities. Whether it's double selling or stockouts, you are likely to lose revenue and customers. Return customers may also drop in if they receive incorrect orders. Manual processes, human errors, and outdated systems may result in inaccurate inventory data.
The need of the hour is warehouse inventory systems that offer real-time updates and an integrated Order Management System (OMS). This way, your warehouse can replenish stocks on time and avoid overselling. In fact, best-in-class warehouses aim for an order accuracy rate of 99.5-99.9% and a service level (On-Time in full, or OTIF) of at least 98-99%.
A WMS (Warehouse Management System) helps you achieve these benchmarks and ensures real-time inventory visibility. As a result, businesses can enhance efficiency and ensure that customers receive their orders on time, every time.
2. High Operational Costs
Manual processes across warehouses can be highly time-consuming and expensive. Whether it is sorting, picking, or packing, each process requires several steps, verification, and special efforts. In warehouses using older systems, this can be incredibly challenging, as data must be manually entered into the warehouse systems. This further increases labor costs and inefficiencies.
A WMS can help you cut through all this clutter and prioritize important tasks. With automated workflows for each process across the warehouse, today's AI-powered, intelligent warehouse management system helps you lower operational costs and increase revenues.
A McKinsey survey points out how early adopters of AI-enabled supply chain systems improved inventory levels by 35% and service levels by 65%.
3. Slow Order Fulfillment
As e-commerce grows, the importance of instinct and quick fulfillment cannot be forgotten. However, with manual processes and older warehouse systems in play, order fulfillment may suffer significantly. This is exacerbated by wrong orders being sent and returns increasing, leading to profit and opportunity loss. A WMS streamlines the order processing workflow, from picking to packing and shipping, ensuring faster and more accurate order fulfillment.
A warehouse management system helps transform operations by solving these significant hurdles.
The Inner Workings of a WMS Explained
A Warehouse Management System, or WMS, is like the brain behind your warehouse operations. It brings everything together—from inventory tracking to order fulfillment—into one smooth, connected system. Let’s break down how it actually works in real life:
Inventory Management
Your WMS keeps a real-time record of everything in your warehouse—what you have, how much of it, and exactly where it’s stored. This helps avoid stockouts, overstocking, and wasted space. Think of it as a smart inventory assistant that never sleeps.
Order Processing & Fulfillment
When a customer places an order, the WMS jumps into action. It integrates with your order management system (OMS) to create intelligent pick lists based on where items are stored and the urgency of the order. This makes picking faster and reduces wasted movement around the warehouse.
Receiving & Put-Away
As new stock comes in, the WMS helps verify that everything matches the purchase order. Then, it guides items to the best spot in the warehouse, following rules you've set in advance. In many modern warehouses, robots even handle this part—making it faster and more accurate.
Shipping
Once an order is ready, the WMS generates shipping labels and paperwork. It ensures that each package meets both carrier requirements and customer preferences, allowing deliveries to go out smoothly and on time.
Reporting & Analytics
The best WMS platforms don’t just help with day-to-day tasks—they also give you the insights you need to improve. From performance metrics to real-time reports, you’ll have the data to make smarter decisions and keep operations running at their best.
How to Choose the Right Warehouse Management System for Your Business
Selecting the best warehouse management system for your business can be a tough challenge. With numerous WMS solutions available on the market today, it can be challenging to determine which one will work best for your company. To help you along, we have compiled a list of key factors you need to look into when picking your WMS:
Functionality and Essential Features
Your ideal WMS should include these essential features:
- Real-time inventory tracking
- Order processing and fulfillment optimization
- Receiving and put-away management
- Picking and packing optimization
- Shipping and carrier integration
- Reporting and analytics
- Customizable workflows
With specific features your business needs, such as batch tracking, cross-docking, or multi-location management, your ideal WMS can help you optimize operations seamlessly. Your warehouse management solution should be flexible and adapt to your needs, whether you manage a single warehouse or multiple distribution centers. You want to look for systems that can automate routine tasks. You also want to ensure your WMS provides real-time data to streamline your warehouse operations.
What to Look for While Choosing a WMS
Scalability & Future Proofing
If you are a small or medium-sized business looking to expand operations, you also need a WMS that grows with you. Therefore, select a warehouse management system that can accommodate increased order volumes and support the addition of new warehouses in the future. You must also ensure that your WMS is conversant with emerging technologies, including the latest versions of AI, machine learning (ML), and robotics.
Integration Capabilities
The best WMS you can choose for your business should seamlessly integrate with your existing ERP, e-commerce platforms, and transportation management systems. Your WMS should offer some level of integration with accounting and CRM systems to ensure that updates related to inventory costs, returns, and payments are made where necessary.
However, the degree of integration will depend on your business model. For instance, some companies may rely on ERP systems for handling accounting, and direct CRM integration might only be required if the sales process is closely tied to warehousing operations. It must also offer mobile app connectivity to your staff and key stakeholders for easy real-time visibility.
Vendor Reputation and Support
When you're investing in a new warehouse management system, you're not just buying software—you're starting a long-term partnership. Therefore, it’s essential to select a vendor you can trust. Look for a provider with a solid reputation, proven experience, and a responsive support team that has your back when things get tricky.
It also helps to know how flexible the system is. Can the vendor customize the WMS to fit your unique needs? Do they offer regular updates? And how smooth is the setup process? Be sure to ask about implementation timelines, training requirements, and the system's overall user-friendliness. Reading customer reviews, case studies, and even asking for referrals can give you a much clearer picture.
Cost vs. ROI
Investing in a WMS (or any ERP solution) is a big decision—and a long-term one. So don’t just think about the upfront cost. Think about the return on investment it can deliver over time.
Here are a few key cost areas to consider:
- Software licensing
- Implementation and setup
- Ongoing support and maintenance
- Hardware (if needed)
- Training for your team
A great WMS should help you save time, reduce errors, and lower labor costs, all while improving order accuracy and customer satisfaction. That’s what turns a cost into a wise investment.
Security & Compliance
Data security isn’t optional—it’s essential. Your WMS should come with strong encryption, access controls, and audit trails to protect your warehouse and customer data.
Ensure the system complies with industry regulations, especially if you handle sensitive data or work in a regulated industry. Look for compliance with standards such as GDPR or HIPAA, depending on your region and industry sector.
How Omniful WMS Solves Warehouse Management Challenges
Omniful's (WMS) warehouse management system is designed to address the complex challenges of modern warehouse operations. Its core features include:
Advanced Inwarding:
From inventory tracking for real-time visibility into stock levels and locations to ensuring accurate inventory management. Omniful's WMS ensures all processes of managing incoming inventory are automated and streamlined. This includes optimizing gate entries, generating precise Gene Regulatory Networks (GRNs), and streamlining putaway processes.
Smart Picking:
With AI-powered Smart Picking, Omniful's WMS integrates route optimization, zone classification, and intelligent inventory management to enhance efficiency. This helps create seamless workflows that increase efficiency.
Cycle Count:
With Omniful’s WMS, you don’t have to wait for a big annual inventory check. Its cycle count feature lets you run both scheduled and surprise counts anytime. This means your stock levels stay accurate in real-time, making it easier to spot and fix discrepancies quickly—so you're always working with reliable data.
Advanced Outward Processes:
Fulfilling orders doesn't have to be a race against the clock. Omniful’s WMS uses intelligent algorithms to create the most efficient picking routes, saving time and reducing errors. From picking to packing and shipping, you can manage all outward operations smoothly and with less manual effort.
Multi-Hub Management:
Running more than one warehouse or fulfillment center? No problem. Omniful’s WMS makes it easy to oversee multiple hubs from a single platform. You get a clear view of everything, all in one place—making scaling your operations simpler than ever.
Optimize Your Warehouse Today with Omniful WMS
Effective warehouse management is more than just moving boxes—it's the backbone of a smooth, efficient supply chain. By implementing an effective warehouse management system, leveraging automation, and adopting best practices, you can significantly reduce errors, lower operational costs, and improve order accuracy.
Remember, a well-managed warehouse creates a ripple effect that benefits your entire supply chain — from suppliers to customers. Investing time and resources in optimizing your warehouse management will help you respond more quickly to market demands, maintain better inventory control, and ultimately increase your business’s profitability.
Are you jealous of how your competitors are managing it all? Book an Omniful demo today and optimize your warehouse management like never before!
FAQs
1. What does a Warehouse Management System (WMS) actually do?
Think of a WMS as your warehouse’s brain. It helps automate and streamline everyday tasks, keeps track of inventory in real time, and boosts overall efficiency. It’s the key to running a smarter, faster operation.
2. How can I make better use of my warehouse space?
Start by utilizing vertical storage, use dynamic slotting to position items where they make the most sense, and consider cross-docking to minimize storage time. A WMS can also help by showing you exactly where to place items for maximum space efficiency.
3. What are the biggest challenges warehouse managers face today?
Some of the top issues include maintaining accurate inventory, meeting high-speed delivery expectations, controlling labor costs, and adapting to the rapid pace of e-commerce. It's a lot to juggle, which is why smart tools like WMS are becoming essential.
4. How can I ensure my warehouse remains safe and accident-free?
Safety begins with regular training and maintaining equipment in optimal condition. However, layout matters too—a clean, well-organized warehouse reduces the risk of accidents. A WMS can also help by reducing clutter and directing smarter workflows, making your space safer for everyone.
5. Can Omniful’s WMS integrate with my other supply chain tools?
Absolutely. Omniful’s WMS solution easily integrates with ERP systems, shipping software, and e-commerce platforms to create a seamless supply chain and logistics network.
6. How do I know if my existing WMS needs an upgrade?
Look out for signs such as frequent inventory errors, delayed shipments, manual processes, and a lack of real-time data that can create barriers, including errors, high costs, and delayed orders. Upgrading to a modern AI-driven WMS, such as Omniful, can resolve these issues and boost performance.