Warehouse Operations: Process, Workflows, & Resources
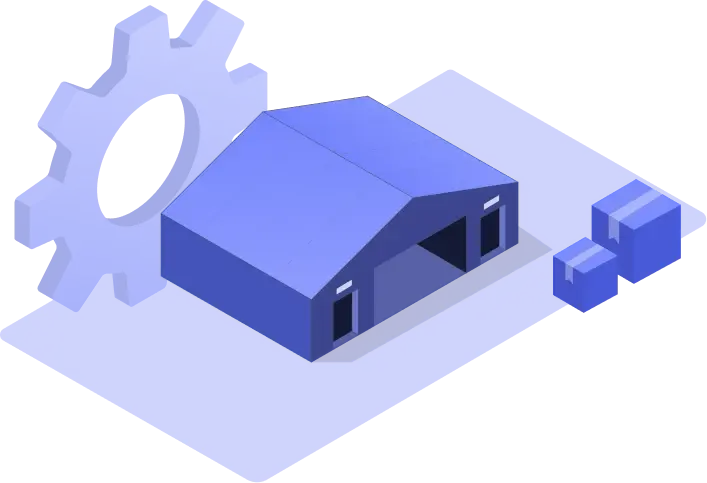
Table of Contents
An effective warehouse operation forms the backbone of a successful supply chain operation and business efficiency. In this context, warehouse operations involve a complex combination of interdependent components working seamlessly to ensure that there is smooth product flow and adequate resource utilization. In fact, its core lies in inventory management, which serves as a critical foundation for achieving excellence in operations and delivering orders to customers.
Effective Role of Inventory Management
Warehouse operation management is the core element of inventory management. The process helps a business manage optimal stock levels at low costs. By using tight inventory control, a warehouse can avoid stockouts and reduce excess holding costs, maximizing storage space usage. In any business, customer satisfaction is closely related to the efficiency of warehouse operations and thus affects profitability.
Optimize Warehouse Operations For Workflow
Businesses will need to implement standardized operating procedures, which cover every aspect of inventory movement and control. Warehouse workflow optimization is, therefore, ensuring that processes from receiving through shipping have each step of the way contributing to making them efficient. Modern warehouse operations are also increasingly dependent on automation and digitization for reducing human efforts and for precision.
Important Performance Metrics
The successful operation of the warehouse is dependent on tracking key metrics and KPIs. Some important measurements include:
- Receiving efficiency
- Accuracy in picking orders
- Inventory accuracy
- Put-away time
- Order lead time
Supply Chain Integration
Warehouse operations should be integrated with overall supply chain management strategies for the right inventory levels and to meet the order at the right time. This integration will enable real-time tracking of the movement of inventory and help in quick response to changes in market demand.
Cost Control Measures
Proper warehouse operations control costs and eliminate unnecessary wasteful expenses. It focuses on optimizing storage space and handling costs while minimizing carrying costs through effective inventory systems. Proper warehouse operations management helps businesses significantly reduce direct operating expenses without sacrificing levels of service.
Planning and Organizing Your Warehouse for Maximum Efficiency
A well-designed warehouse layout serves as the foundation for streamlined operations and enhanced productivity.
Designing an Efficient Warehouse Layout
The layout must incorporate distinct zones for receiving, storage, picking, packing, and shipping to optimize warehouse operations. An efficient warehouse layout minimizes handling times and enhances overall workflow by strategically positioning high-demand items near shipping areas. Three primary layout designs - I-shaped, U-shaped, and L-shaped configurations - offer different advantages for warehouse workflow optimization.
Creating Optimized Storage Zones
Storage optimization requires implementing strategic solutions like ABC analysis, where inventory is categorized based on movement frequency. Vertical storage solutions and mezzanine floors maximize space utilization without expanding the warehouse footprint. Automated Storage and Retrieval Systems (AS/RS) further optimize warehouse operations by enhancing vertical space usage and improving order accuracy.
Traffic Flow Analysis
Warehouse workflow optimization depends heavily on efficient traffic patterns. The layout should reduce unnecessary movement within the warehouse by minimizing travel distances between different operational areas. Strategic placement of pick and pack stations near frequently accessed items can significantly improve warehouse operations efficiency.
Order Fulfillment Best Practices
To streamline order fulfillment, warehouse operations should incorporate automated processes to prevent picking errors and enhance accuracy. Implementing batch picking for slow-moving items and utilizing pick-to-light systems can significantly reduce travel time and optimize warehouse operations.
Environmental Controls
Climate-controlled warehouse systems play a crucial role in maintaining product quality. These systems incorporate temperature control, humidity management, and air quality monitoring to ensure optimal storage conditions. Modern warehouse operations often include automated environmental control systems to maintain consistent conditions throughout the facility.
Dock and Yard Management
Effective yard management strategies are essential for optimizing warehouse operations. This includes implementing robust scheduling systems for loading and unloading, coordinating transportation resources, and maintaining clear communication channels between yard personnel and carriers. Real-time asset tracking and visibility systems help reduce delays and improve overall yard productivity.
Warehouse Management Systems to Success
Warehouse complexities in managing their inventories and order fulfillments create the need for more involved systems and processes to service such demands in modern warehousing.
Implementation of a Warehouse Management System
A standard WMS implementation usually lasts 4-6 months, and is divided into five key phases to optimize warehouse operations. The whole process begins with documenting the operational processes and identifying the requirements for specific functionality. Software setting configuration, master data configuration for SKUs, and integration with existing systems have been successful warehouse management strategies.
Inventory Tracking and Management Techniques
Advanced warehouse operations utilize multiple inventory management approaches:
- ABC Analysis will help in categorizing products based on value and movement frequency
- Perpetual inventory management enables real-time counting through the use of RFID and POS systems
- Batch tracking tracks expiration dates and quality control measures
- FIFO/LIFO systems ensure proper stock rotation and tax optimization
Regular Stock Audits
Stock audits are part of warehouse management plans that help to balance the accounts with the physical inventory on hand. These stock audits avoid wasteful overstocking, identify obsolete stock, and reduce financial loss. Regular auditing helps in accurate record keeping of the stock and supports optimal operations within the warehouse. Demand Forecasting and Planning Currently, warehouse operations rely on AI-based statistical modeling that will predict the future needs of customers. This strategy has enabled organizations to be able to:
- Manufacture
- Resource
- Procure
Inbound and Outbound Logistics
Quality Control Procedure
Quality control techniques form an integral part of warehousing management policies. Regular checking of goods coming and leaving the warehouse, putting into place cross-checks and setting standards for products can be put in place. Proper documentation and routine preventive maintenance ensure that the warehouse workflow optimization process always occurs.
Role Of Technology In Modern Warehouse Operations Advanced Technology
Modern warehouses are being transformed to significantly increase efficiency and productivity in warehouse operations. Smart warehouse technologies integrate automation, artificial intelligence, robotics, and IoT to create seamless environments driven by data, maximizing all aspects of warehouse operations.
Utilizing Automation for Improved Operations
Warehouse automation reduces human interaction and centralizes and accelerates activities taking place in the warehouses. Automated systems allow warehousing to optimize its inventory, increasing the accuracy of the filled orders and reducing operating expenses. Autonomous Mobile Robots travel through warehouse spaces and locate goods, transport, and optimize routes using sensors fitted with AI.
Warehouse Robotics for Higher Productivity
Robotics technology changes conventional warehouse operations by performing repetitive tasks more accurately and at a faster pace. The latest models of warehouse robots that incorporate AI and machine learning can adapt to new environments. Therefore, they simplify order fulfillment and inventory control processes. These systems enhance productivity and reduce physical labor for human workers.
IoT and Real-Time Data Integration
IoT devices used in warehouse management allow operations to be monitored and followed in real-time. Smart sensors scan the inventory levels, machine status, and environmental factors and enable warehouse managers to make decisions immediately. In this way, connectivity with inventory tracking, the monitoring of equipment, and overall operational efficiency are upgraded.
Mobile Technology Integration
Mobile devices transform warehouse management by allowing remote monitoring and control of operations. Specific warehouse management apps can provide the employee with real-time access to information, eliminating the need for paper-based systems and minimizing errors. It will make communication between the teams and managers in warehouses smooth and enable faster decision-making with better productivity.
Applications of AI and Machine Learning
AI-based systems will analyze large amounts of data to optimize inventory management and predict demand patterns. It improves predictive maintenance, demand forecasting, and route optimization using machine learning algorithms. Quality control and asset tracking improve by using computer vision systems. This allows warehouses to be human-independent while maintaining high accuracy levels.
Cloud-Based Warehouse Management
The flexibility afforded by cloud-based warehouse management systems allows for instant accessibility to data from anywhere that promotes coordination across several locations. Such flexibility would present the manager with an up-to-date view of inventory levels and allow tracking of shipments together with instant adjustments to labor allocation to make operations in a warehouse more efficient. Cloud-based solutions also reduce infrastructure expenses but ensure robust security measures along with scalability options.
Safety and Compliance in Warehouse Operations
Safety and compliance form the cornerstone of successful warehouse operations, requiring systematic protocols and rigorous implementation. Proper safety measures not only protect workers but also optimize warehouse operations by preventing accidents and minimizing downtime.
Safety Protocols Implementation
Warehouse operations must incorporate comprehensive safety measures, including proper PPE usage, mandatory safety signage, and hazard communication programs. A robust warehouse management strategy includes implementing fire prevention plans and establishing clear emergency action protocols. Regular safety observation checks ensure compliance with established protocols and maintain optimal warehouse workflow optimization.
Equipment Safety Training
Staff training represents a crucial component of warehouse operations safety. This includes forklift operator certification, hazardous material handling procedures, and proper ergonomics training. Workers must receive adequate safety training from qualified instructors before operating any warehouse equipment.
Equipment Maintenance
Scheduled maintenance plans are essential for all warehouse equipment. Replacement dates for machinery components should be recorded and followed strictly to enhance equipment life and condition. For specialized equipment, annual maintenance contracts with manufacturers ensure proper upkeep and optimize warehouse operations.
Emergency Response Planning
Every warehouse requires a comprehensive emergency response plan that includes:
- Evacuation procedures and assembly points
- Emergency contact lists
- First aid kit locations
- Up-to-date fire extinguishers
- Designated emergency leadership roles
Regulatory Compliance
Warehouse operations must adhere to various regulatory standards, including OSHA requirements, environmental regulations, and industry-specific guidelines. This encompasses proper storage conditions, handling procedures, and documentation requirements to ensure legal compliance and operational efficiency.
Environmental Sustainability
Modern warehouse management strategies increasingly focus on environmental sustainability through:
- Energy-efficient systems implementation
- Waste reduction programs
- Water conservation measures
- Renewable energy integration
These initiatives not only support environmental goals but also contribute to optimizing warehouse operations through reduced operational costs and improved resource utilization.
Conclusion
Modern warehouse operations require a strategic blend of technology, efficient processes, and skilled management. Omniful's comprehensive warehouse management solution addresses these needs by offering cutting-edge features that optimize warehouse operations and streamline workflows. From inventory management to automated picking processes, Omniful's platform integrates seamlessly with existing warehouse management strategies to enhance productivity and reduce operational costs. By implementing these foundational principles alongside Omniful's innovative solutions, warehouses can achieve superior operational efficiency and maintain a competitive edge in today's dynamic market.
FAQs
What are the most critical metrics for measuring warehouse operations performance?
Key metrics include order accuracy rate, inventory turnover ratio, picking accuracy, on-time shipping performance, and labor productivity rates. These indicators help optimize warehouse operations and identify areas for improvement.
How can warehouse workflow optimization be achieved with minimal investment?
Start by implementing basic warehouse management strategies such as ABC analysis, optimizing layout design, improving inventory accuracy, and training staff properly. These foundational improvements can yield significant results before investing in expensive technology.
What role does automation play in modern warehouse operations?
Automation streamlines repetitive tasks, reduces errors, increases processing speed, and improves accuracy in picking, packing, and inventory management. It serves as a crucial component in optimizing warehouse operations.
How often should warehouse safety training be conducted?
Safety training should be conducted during initial onboarding, quarterly refresher sessions, and whenever new equipment or procedures are introduced. Regular training ensures compliance and maintains efficient warehouse operations.