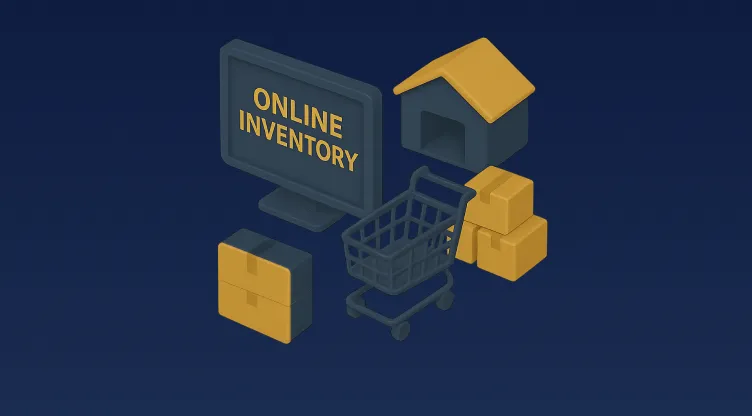
Online inventory management is the process of tracking the physical inventory of your business. The tool can be cloud-based, or it can be a software system that uses your resources rather than relying on the cloud for managing the inventory levels, orders, sales, and deliveries in real time, which is particularly needed in retail inventory control and e-commerce inventory management.
Read More10 Min Read
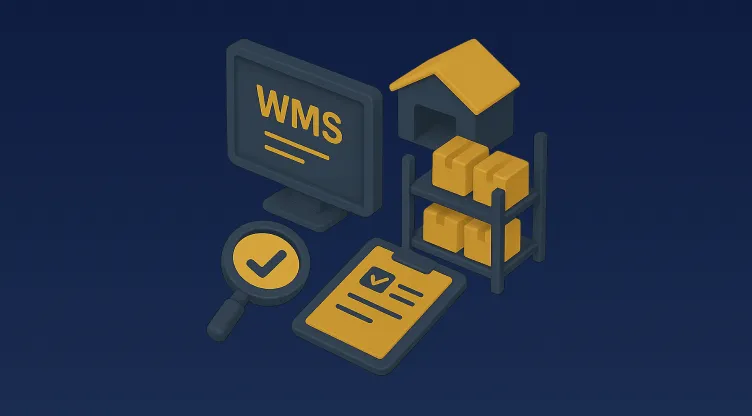
Due to supply chain disruptions and labor shortages, retailers, manufacturers, and other omnichannel players constantly struggle to adapt. In fact, according to a report, some of the biggest challenges facing supply chain operations include talent shortages (56%), disruptions (54%), running out of stock (52%), and consumer demands (52%).
Read More14 Min Read
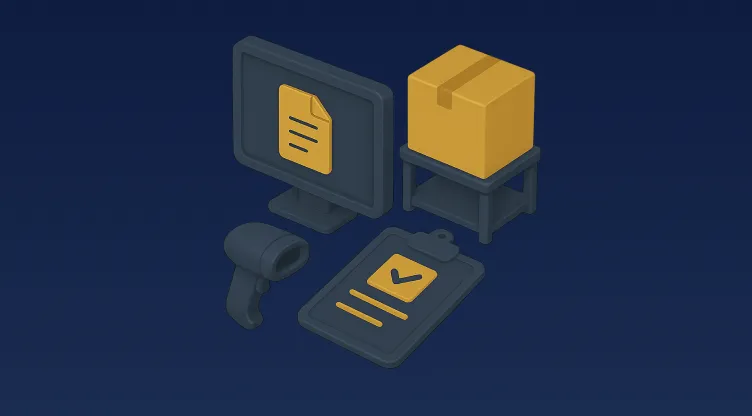
The growth of eCommerce is constantly changing the way international trade works. With 2.71 billion people shopping online globally as of 2025, 33% of the world's population is hooked to multi-channel eCommerce experiences. For companies, this translates into a constant struggle to maintain orders from various eCommerce channels and other sources to ensure they reach consumers on time. This is where the world’s best order management systems come into play.
Read More11 Min Read
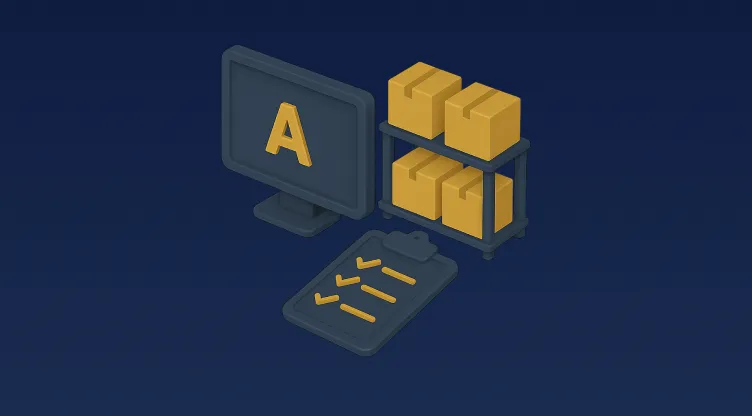
As online and digital shopping becomes more mainstream, companies are hard-pressed to gain consumer attention. One of the aspects that differentiates the high-performing eCommerce players from other businesses is delivery timing. If your online shop is unable to satisfy customer needs for instant gratification and quick delivery, the chances of losing out on repeat business increase.
Read More11 Min Read
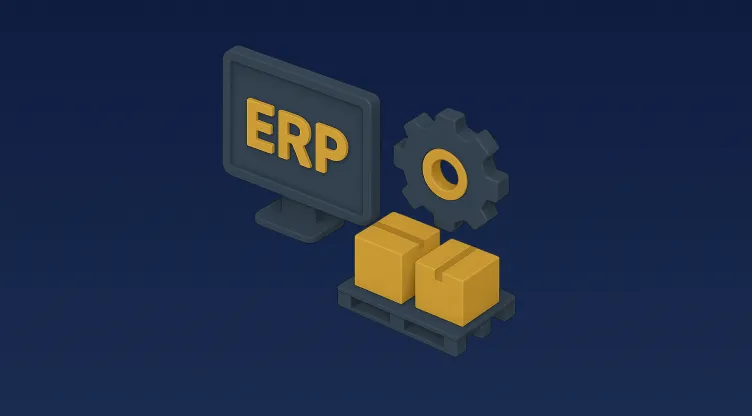
As businesses scale and grow, multiple functions and departments come into being. Managing all the different functions of a growing business requires strategic planning and management. This is where top ERP systems come into play. An enterprise resource planning and management software will help all your teams manage several tasks in an organized manner. Modern ERP systems further leverage Web 4.0 to ensure connectivity across all functions and systems, providing businesses with one central hub where all activity can be monitored and managed.
Read More11 Min Read
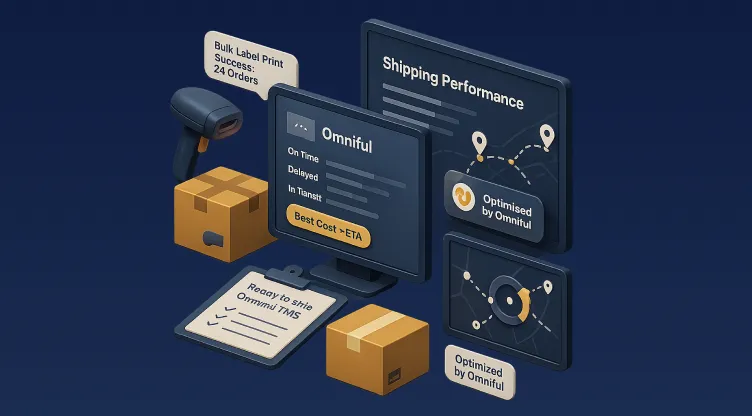
Efficient warehouse shipping operations ensure uninterrupted order processing and shipping activities.
Read More8 Min Read
It does look easy from the outside to get a product from the warehouse and deliver it to the customer. However, it involves many steps that can make a big difference. Order fulfillment is how businesses handle everything. It manages everything, from getting orders to delivering them. This e-commerce fulfillment process is absolutely critical for online businesses because it helps deliver orders on time and in good condition.
Read More7 Min Read
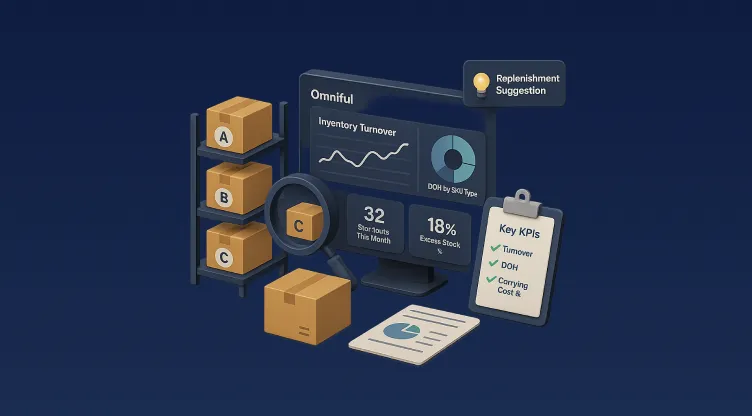
Inventory analysis is the systematic evaluation of a company's stock levels, movements, and management practices.
Read More8 Min Read
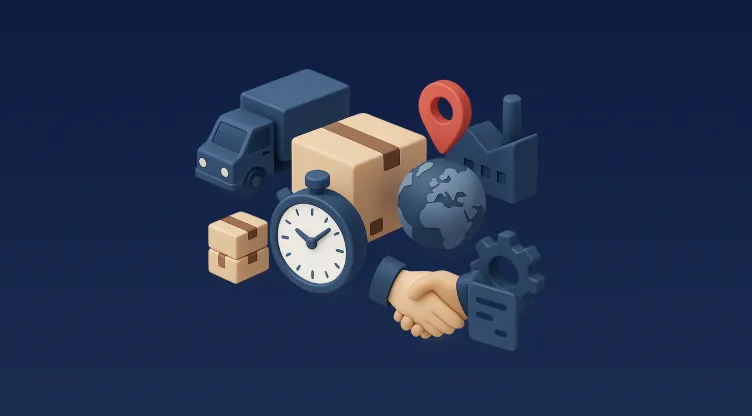
Learn how to cut inventory lead times by improving supplier collaboration, using faster shipping methods, and sourcing locally. Tailored for MENA region supply chains.
Read More5 Min Read